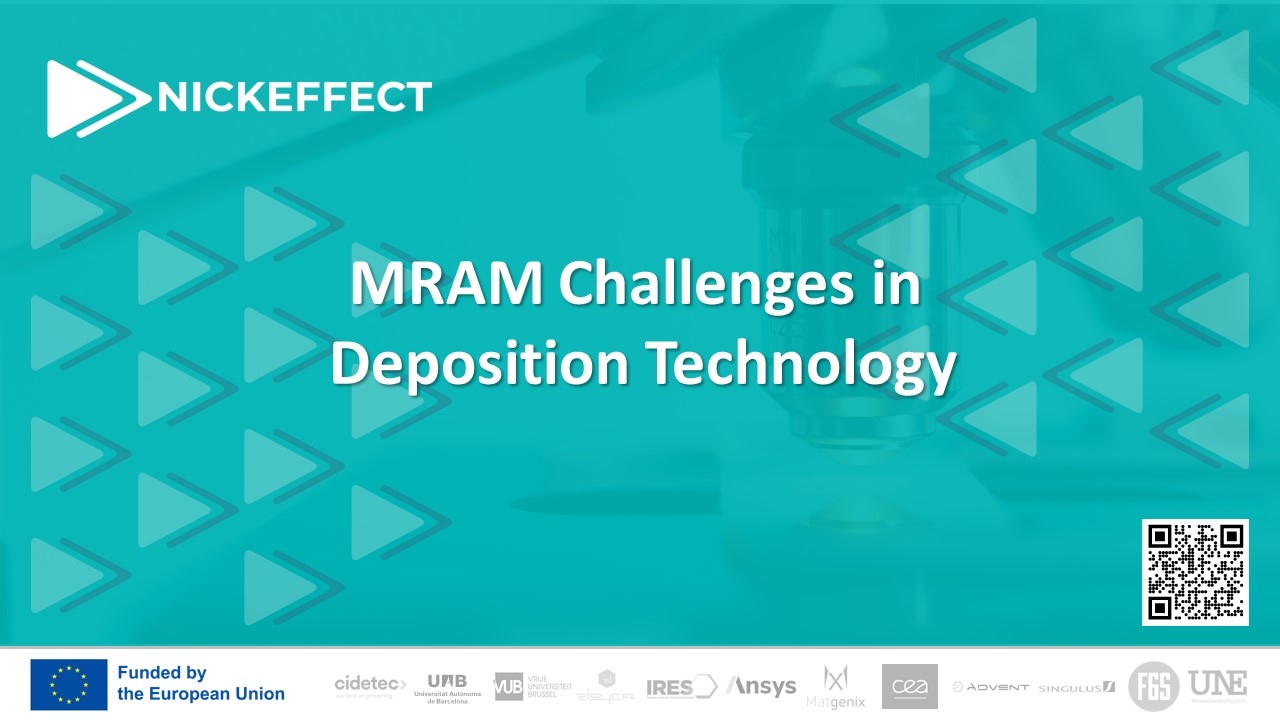
Magnetoresistive random-access memory (MRAM) technology is one of the current methods for memory storage.
Its advantages over earlier storage devices lie in the fact that here high speed, high density as well as low power consumption are combined to provide a nonvolatile robust mechanism for data storage.
Unlike earlier memory devices, MRAM technology uses magnetic information to store data. Basically, the structure consists of two ferromagnetic thin layers separated by an ultrathin insulating dielectric layer which usually is MgO. This results in a magnetic tunnel junction (MTJ). The device makes use of the fact that electrons also carry a spin beside a current.
Put simply, in a ferromagnetic layer, the electrons align their spins parallel to the direction of magnetization. Electrons with their corresponding spin of this layer can pass through the insulating layer easily if the magnetic alignment of the second ferromagnetic layer is parallel to the first layer. This results in a measurable low electrical resistance. Consequently, in case of an anti-parallel orientation the measured resistance is high. This is called tunnel magneto resistance (TMR) effect.
To use the device as a storage element, one of the ferromagnetic layers needs to retain a fixed magnetic orientation as a reference and one layer is free to get switched. Classically, to obtain a stable reference layer, it was attached to a layer consisting of a rather thick antiferromagnetic material.
For the need of downsize in modern devices, nowadays artificial antiferromagnets (AAF) are used. This hard magnet consists of a laminated layer system of (Pt/Co)n / Ru / (Pt/Co)m (where n and m state the number of repetitions).
All multiple layers of the device, the ferromagnetic, the insulating and the layers for the antiferromagnetic hard magnet need to be ultrathin in the range of 1nm and below.
On a production scale for layer stacks on 300mm wafers this is best achieved through, Physical Vapor Deposition (Sputtering). These exacting preconditions also necessitate a precise large area control for thickness and uniformity.
Here, the SINGULUS cluster tool platform comes into play with its expertise to address various magnetic applications. Depending on requirements for the process and the layer stack recipes the cluster modules can build very precise layer stacks with thicknesses ranging from a fraction of a nm up to several μm on the wafer.
Low power consumption and the possibility to sputter up to 12 materials in one vacuum chamber without any transfer of the wafer between different chambers minimize the time between depositions of two subsequent layers. Additionally, the full scope of techniques such as: DC-, pulsed DC- and RF-magnetron sputtering as well as combinations of these modes allow the deposition of both metallic and dielectric materials.
Now, part of the NICKEFFECT project aims at developing alternative artificial antiferromagnets by substituting Pt with Ni. Pt is in high demand due to its proven unique properties for the semiconductor industry. Aside from the high price, considering that 80% of world production is concentrated in two countries, South Africa and Russia, the risk for disruption in supply explains the classification of Pt as a critical raw material (CRM) in terms of procurement.
Obviously, as an element with a ferromagnetic character and abundantly present in the earth, Ni could be a possible candidate and poses no risk of shortage or interruption of supply. Therefore, substituting Pt with Ni may prove to be important and essential for the EU economy to promote raw materials value chains for the application in key industrial sectors.
In this context, SINGULUS TECHNOLOGIES applies its expertise and its cluster tool to develop and test alternative Co/Ni multilayer stacks to replace the currently predominantly used Pt/Co layer stacks. Should the results prove to be successful these novel AAF structures in future, may play an important role in applications such as storage, sensing and artificial intelligent (AI).