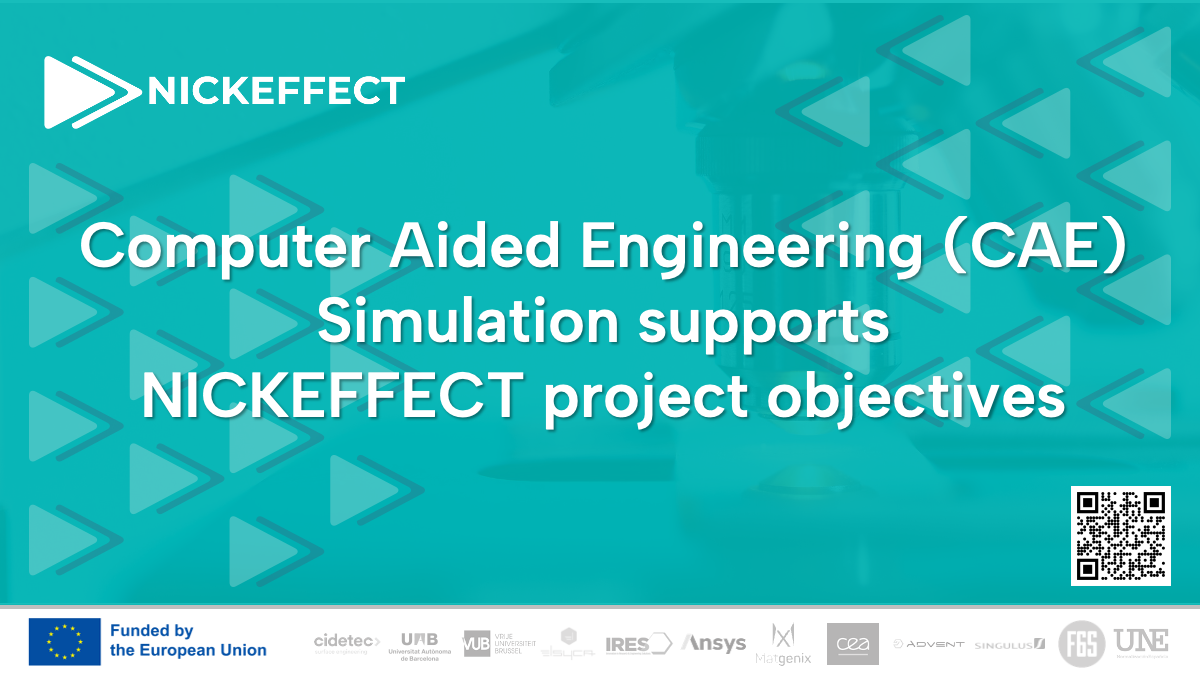
Computer Aided Engineering (CAE) simulation supports NICKEFFECT project objectives
The NICKEFFECT project has identified an opportunity to replace platinum group metals in key applications such as electrolysers fuel cell catalysts and magneto-electronic devices. The proposed alternative is based on nickel (Ni), an earth-abundant element with a ferromagnetic character.
Platinum group metals have unique characteristics (unreactive, resistant to corrosion, stable at high temperatures) that make them indispensable in different strategic sectors such as renewable energy, electric mobility and digital technologies. These properties make platinum group metals ideal as a catalyst for chemical and electrochemical reactions.
To replace platinum-coated electrodes by using a Nickel-based alternative, the electrodes should have a much higher active surface for reaching equivalent performance. One way to achieve such an increased active surface is to create a porous micro-structure with a high surface-to-volume ratio. Indeed, the higher surface-to-volume ratio provided by the increased porosity will allow enhancing the catalytic performance or the Converse Magnetoelectric Effect (CME) in electronic devices. The manufacturing of such high surface-to-volume ratio Ni structures is enabled by using an advanced electroforming technique.
In practice, an electroplating process can be used to create lightweight porous Ni-based thin coatings from a packed bed.
On the use of Computer Aided Engineering
Computer Aided Engineering (CAE) relies on the use of computer software to replicate in a digital environment a design or a process. This digital twin concept is used across many industries and applied to simulate, validate and optimize products, processes, and manufacturing tools. In the framework of the NICKEFFECT project, the use of a Computer Aided Engineering solution aims at improving the manufacturing process of Ni-based porous electrodes.
The electroforming process of such electrodes is indeed very sensitive to numerous parameters such as metal ion bulk concentrations, imposed current regime (pulse, pulse reverse, DC, …), agitation regime and packed bed characteristics (morphology, thickness). All of these parameters impact the electroforming process and the final alloy composition of the deposited metal structure.
As a result, the alloy composition might change significantly over the thickness of the packed bed, thereby compromising the final performance of the porous electrode structure when functioning as a Hydrogen Evolution Reaction (HER) cathode in a Water Electrolysis (WE) cell.
Being able to better understand and quantify the impact of these parameters on the final quality of the manufactured electrode is therefore key to ensuring the ultimate objective of the NICKEFFECT project in replacing Pt group metals with nickel alloys.
This is where Elsyca brings its electrochemical modelling expertise to the NICKEFFECT consortium. Elsyca has extended its longstanding PIRoDE software platform, a versatile tool for investigating electrochemical deposition processes via 1D simulations at a Rotating Disc or Rotating Cylinder Electrode.
It supports an entirely versatile definition of Multi-Ion Transport and Reaction (MITRe) systems, involving multiple electrode reactions (Butler-Volmer, linear) and homogeneous reactions. Simulations can be performed for voltage or current-controlled processes, thereby considering any type of transient signal (pulse, LSV, …). In the framework of the NICKEFFECT project, the PIRoDE software platform has been extended to support packed bed modelling functionality. The model extension allows considering a packed bed of non-conductive particles with a given thickness adjacent to the electrode, whereby the packed bed is modelled with a continuum approach.
As such, PIRoDE can be used in the NICKEFFECT project for modelling the electroplating process of lightweight porous Ni-based thin coatings that are formed from a stacked bed, in turn, to be used in WE cells.
Elsyca PIRoDE therefore can play a crucial role in preselecting and optimizing sets of process conditions to be used for lab experiments aiming at the production of demo WE HER electrodes.