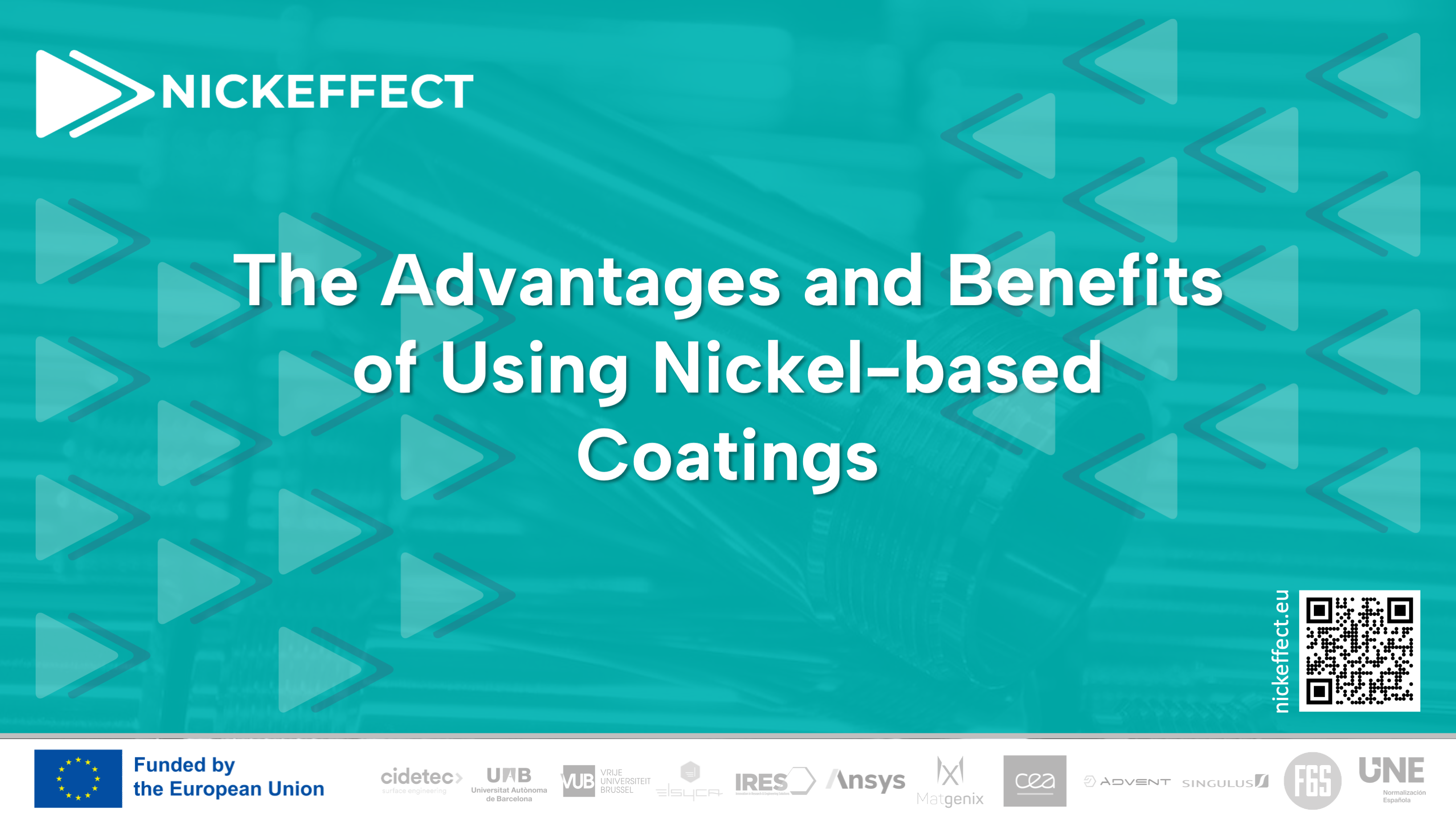
The Advantages and Benefits of Using Nickel-based Coatings
Nickel-based coatings have gained popularity in recent years as an alternative to platinum group metal (PGM)-based coatings, due to their cost-effectiveness, corrosion resistance, thermal stability, hardness, and surface finish. In this article, we will discuss the benefits of using nickel-based coatings and how they compare to PGM-based coatings.
One of the major benefits of using nickel-based coatings is their cost. Nickel is significantly less expensive than PGMs, making nickel-based coatings a more cost-effective option for many applications. This cost advantage can be significant for industries such as automotive and electronics where large volumes of coated parts are needed.
Another important benefit of nickel-based coatings is their corrosion resistance. Nickel has good corrosion resistance in a wide range of environments, making it a suitable choice for applications where exposure to corrosive substances is a concern. This makes nickel-based coatings ideal for use in industries such as chemical processing and marine engineering.
In addition to its corrosion resistance, nickel-based coatings also have good thermal stability and can withstand high temperatures without degrading. This makes them suitable for use in applications where the coated surface will be subject to high temperatures, such as in the aerospace and power generation industries.
Nickel-based coatings also have good hardness and wear resistance, making them suitable for use in applications where the coated surface will be subject to abrasion or mechanical wear. They are also good adhesion to various substrate and easy to be electroplated. This makes them ideal for use in industries such as construction and mining, where coated parts are subject to heavy use and wear.
Finally, nickel-based coatings can produce a smooth and shiny surface finish, making them suitable for use in applications where a high-quality appearance is desired. This makes them ideal for use in industries such as architecture and consumer products where a polished appearance is important.
In this context, the NICKEFFECT project has identified an opportunity to replace PGM-based coatings in key applications such as electrolysers electrodes, fuel cell catalysts and magneto-electronic devices. Furthermore, to enhance the catalytic performance of Ni, innovative deposition techniques to obtain coatings, with ordered and pseudo-ordered porosity, will be developed. The higher surface-to-volume ratio provided by the increased porosity will allow for enhancing catalytic performance or converse magnetoelectric effect (CME) in electronic devices.
In conclusion, nickel-based coatings offer a cost-effective, corrosion-resistant, thermal stable, hard and good surface finish alternative to PGM-based coatings. They are ideal for a wide range of industries and applications, making them a popular choice among engineers and manufacturers. It is also worth considering that the specific application, properties required and the trade-off with costs should be considered before making a choice.